In a recent project, we encountered a challenge with a plant room constructed from SHS members, featuring grating on both the floor and the roof.
Problem 1:
The original structural drawings specified vertical splice plates bolted together. However, these splice plates would protrude through the floor & roof gratings, creating a potential trip hazard.
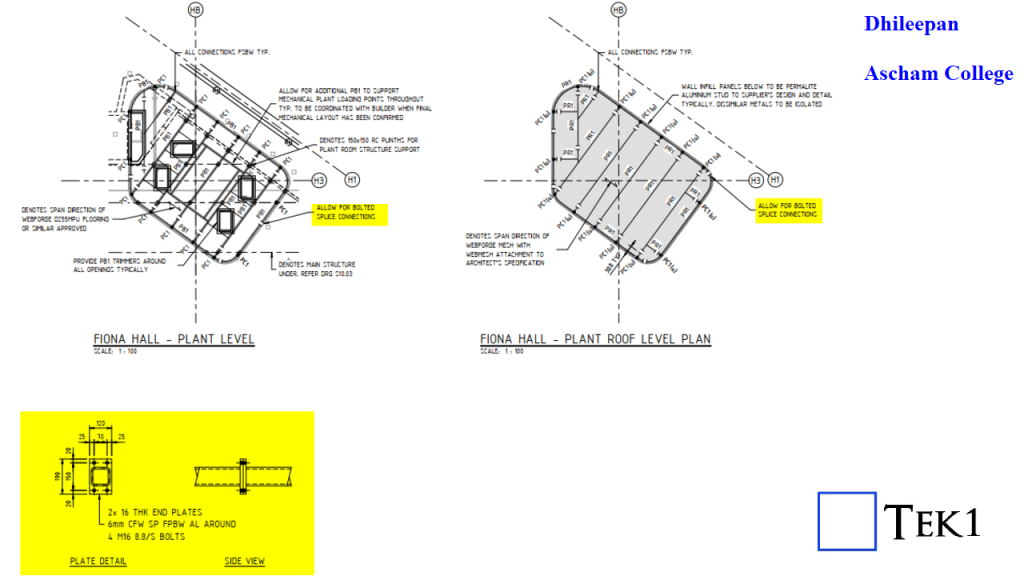
Upon identifying this issue, we notified the structural engineer, who then changed the bolted connections to site-welded connections. While this solution addressed the trip hazard, it introduced a new problem: site welding approximately 40 splices would be both costly and time-consuming.
When this issue was discussed with the fabricator, they proposed shop welding the SHS frames into just two large assemblies for the entire plant room which they had the capacity to transport as large units. This approach significantly reduced the number of site welds required.
Problem 2:
However, another challenge arose: these large assemblies were to be galvanised and were too big for the galvanising bath. We consulted with the fabricator regarding the maximum size of the galvanising bath and suggested subsequently splitting the plant room assemblies accordingly. This adjustment reduced the number of site welds to around 20, making the process more efficient.
Two primary problems were identified and solved:
- The bolted splice causing a trip hazard: Transitioning to welded connections resolved this safety concern.
- Assemblies larger than the galvanising bath: Adjusting the assembly size to fit the galvanising bath ensured the integrity of the galvanising process.
By identifying and rectifying these issues at the planning stage, we saved significant time and money.
If you’re interested in having me (Dhileepan) manage your project, please send a quote request to our principal at koshy@tek1.com.au and mention that you want Dhileepan to manage your project.
Leave a Reply