How we saved our 30% (i.e. hundreds of thousands of dollars) in Costs on the “Emu In the Sky” Project
Recently, we have been detailing one of Australia’s most iconic projects, the “EMU IN THE SKY.” The structure of this project is a 30m globe,
and as part of the steel detailing, numerous connections are involved.
How did we do it?
TEK1 has proposed
- several solutions for the connections required.
- proposed as easy way to acheive more accurate fabrication
- Reduce Fabrication Time
- and ultimately saved the client in the order of hundreds of thousands of dollars.
Hexagon Joint Connections:
The Problem
- This design contains numbers of Hexagon join involved & it required six cruciform connections per hexagon joint. The weight of one Cruciform joint is 60-70kg approx
The Solution
- The TEK1 Team (Ramakrishnan)proposed an alternative solution that reduced the number of cruciform connections required for a hexagon joint..
- By implementing our proposal, we eliminate two cruciform connection per hexagon joint, resulting in substantial savings N-numbers of connections in terms of fabrication.
- This involves saving of Material cost & Fabrication cost.
- Our client was very pleased to see these cost-saving proposals coming from the steel detailer.
- Please refer to the following snaps which showing the detailed info about the proposal
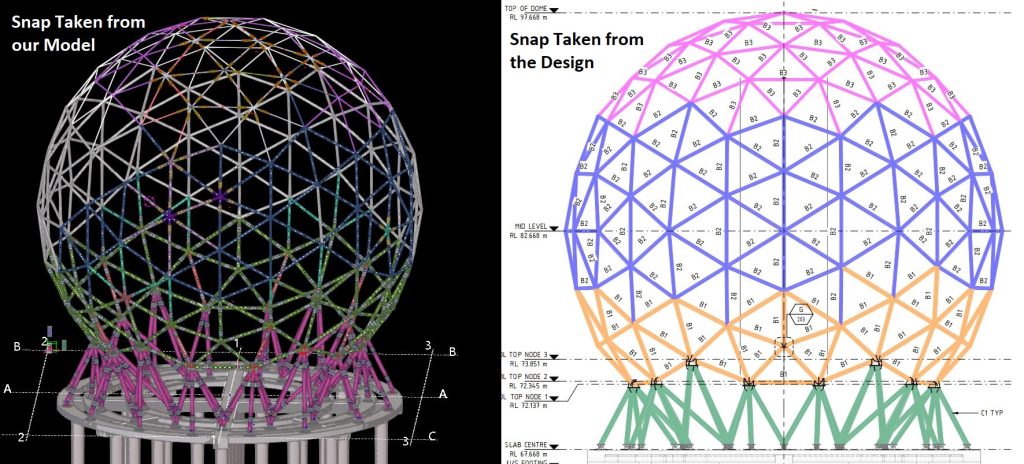
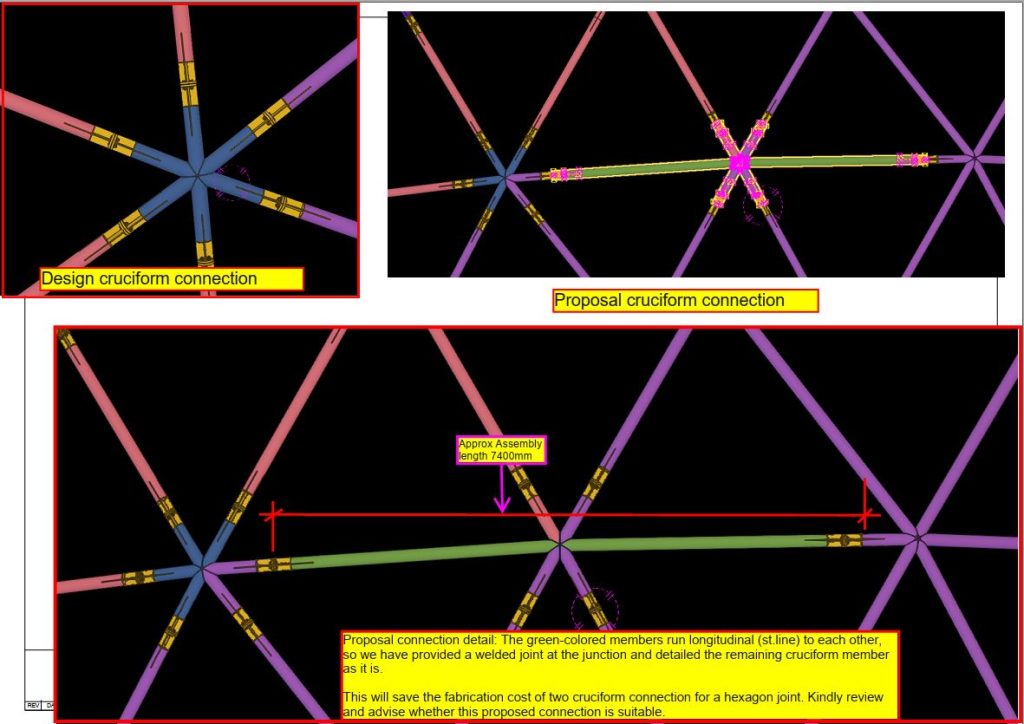
Cruciform Connection Accuracy
The Problem
Another example involves the cruciform design connection, where the initial design called for three 20mm thick plates to be welded
together to form the joint. This connection demands high accuracy in fabrication, as all plates must be perfectly aligned at 90º to avoid
significant erection issues. During welding, there is a possibility of distortion, making it difficult to maintain the desired shape.
This is risky for the client – if they get it wrong they will lose: $abc and lose xyz months
The Solution
To address these challenges, TEK1 proposed a notched cruciform connection. Instead of three plates, we use only two plates, each with a
notch. By interlocking the notched plates, we can avoid steel distortion and achieve the desired design shape more easily. This approach
not only improves fabrication accuracy but also simplifies the assembly process.
Again our client was very pleased to see these cost-saving proposals coming from the steel detailer & we implemented this in our current model.
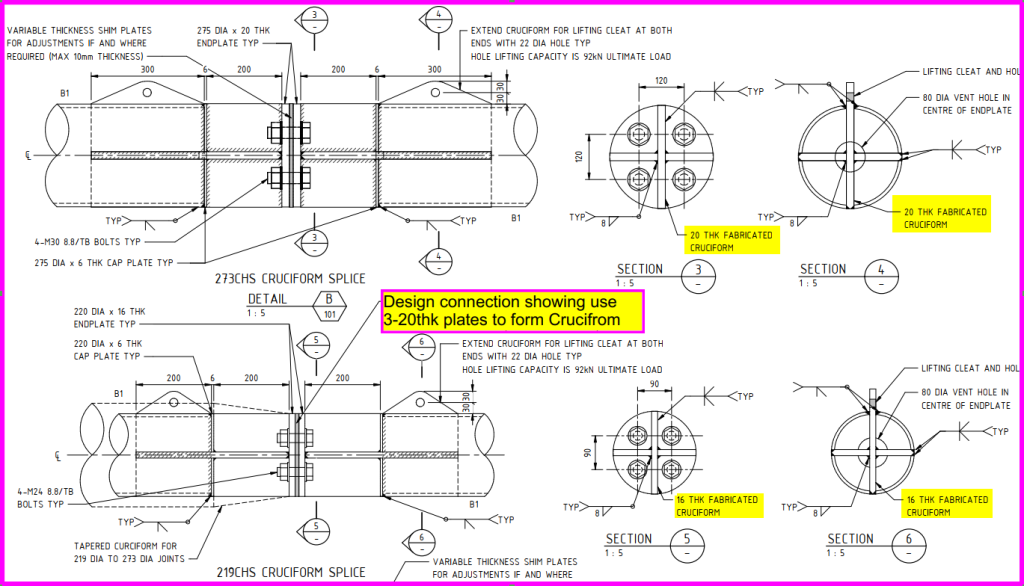
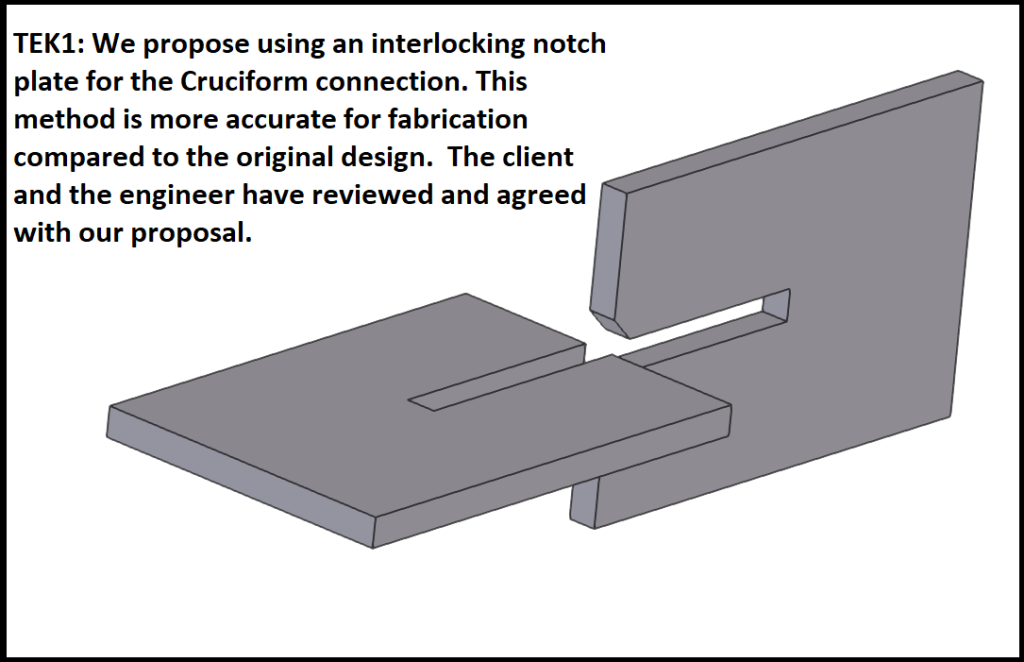
If you’re interested in having TEK1 manage your project, please send a quote request to our principal, Koshy, at koshy@tek1.com.au, and specify that you want Ramakrishnan to manage your project. We look forward to bringing our expertise to your next venture.
Leave a Reply