At TEK1, our extensive experience in detailing bridge projects has equipped us with the knowledge and foresight to minimize rework. Recently, we have been detailing two bridges for a leading company in Australia. Here’s a glimpse into how our expertise can prevent costly mistakes and ensure smooth project execution.
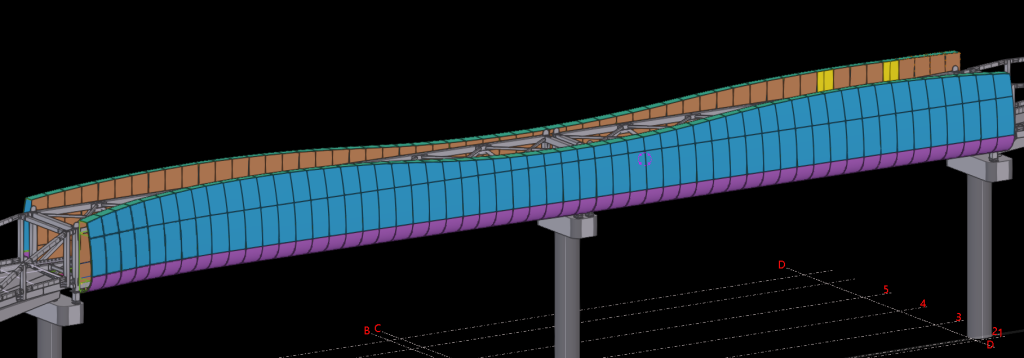
Addressing Cladding Design Challenges
We received design drawings for the cladding around the bridges, one of which showed cladding with only one horizontal split at the bottom location, while the rest was a single piece. However, to facilitate easier handling and reduce the risk of damage, we identified the need for two horizontal splits instead of one.

Why Split the Cladding?
- Handling Issues: Large, single-piece cladding can be difficult to manage in the shop.
- Material Sensitivity: The cladding is made from a small aluminum sheet with perforations, making it prone to damage.
When modeling this type of cladding, it is crucial to consider the fabricator’s handling challenges and potential issues they might face.

TEK1’s Proactive Approach
Given our extensive experience with similar bridge projects, we anticipated these issues. TEK1 arranged for our detailers to visit the factory directly, allowing them to understand firsthand the difficulties fabricators might encounter.
For this particular bridge job, TEK1 proactively raised queries about the maximum length of the cladding before starting the project. By addressing potential issues early on, we can significantly reduce the risk of rework.
The Benefits of Experienced Detailing
By leveraging our experience and proactive approach, TEK1 ensures:
1. Enhanced Efficiency: By identifying and solving potential issues early, we streamline the fabrication process.
2.Cost Savings: Minimizing rework leads to significant cost savings for our clients.
3.Quality Assurance: Ensuring that the design is practical and feasible reduces the likelihood of damage and maintains high-quality standards.
At TEK1, our goal is to deliver projects that not only meet client requirements but also stand the test of time. By understanding and addressing fabrication challenges, we ensure that our detailing work is both precise and practical, ultimately saving time and resources for everyone involved.
Stay tuned for more insights and updates on how TEK1 continues to lead the way in bridge detailing and beyond.
Leave a Reply