Light Gauge vs Wood vs Concrete? Let’s examine the pros and cons:
1. Strength, Durability and Preference:
- LGS: Reasonable strength (for residential loads), resistant to: termites, and rot (but is susceptible to rust – in the long term). Neither wood nor steel does well when exposed to water. Light gauge can be “squeaky”
- Wood: Susceptible to decay, rot and termites. Is very stable.
- Concrete: Very strong. Not commonly used for residential single storey houses.
2. Speed and Cost:
- LGS: Prefabricated off-site, allowing quick assembly on-site. This reduces labour costs and project timelines significantly. LGS is great if your building site is remote, and it is difficult to procure tradespersons: most of the work can be fabricated in a workshop in a metro area – and then transported to the remote location, where it can be assembled with comparatively minimal labour.
- Wood: Often cheaper initially, but long-term costs can rise due to maintenance requirements. The tendency is to cut on site.
- Concrete: Often more expensive due to labour, planning, reinforcement and trucking. Is suitable for high rise structures.
Conclusion
LGS does well in terms of speed of construction. Traditional carpenters who cut and erect on site – may take many months. LGS beats the pants of this mode of construction. Entire houses can be framed in a few weeks. Note: it is also possible to prefabricate wooden frames and erect on site.
Weigh up the costs and benefits accordingly.
At Tek 1, we provide Light Gauge Steel detailing services.
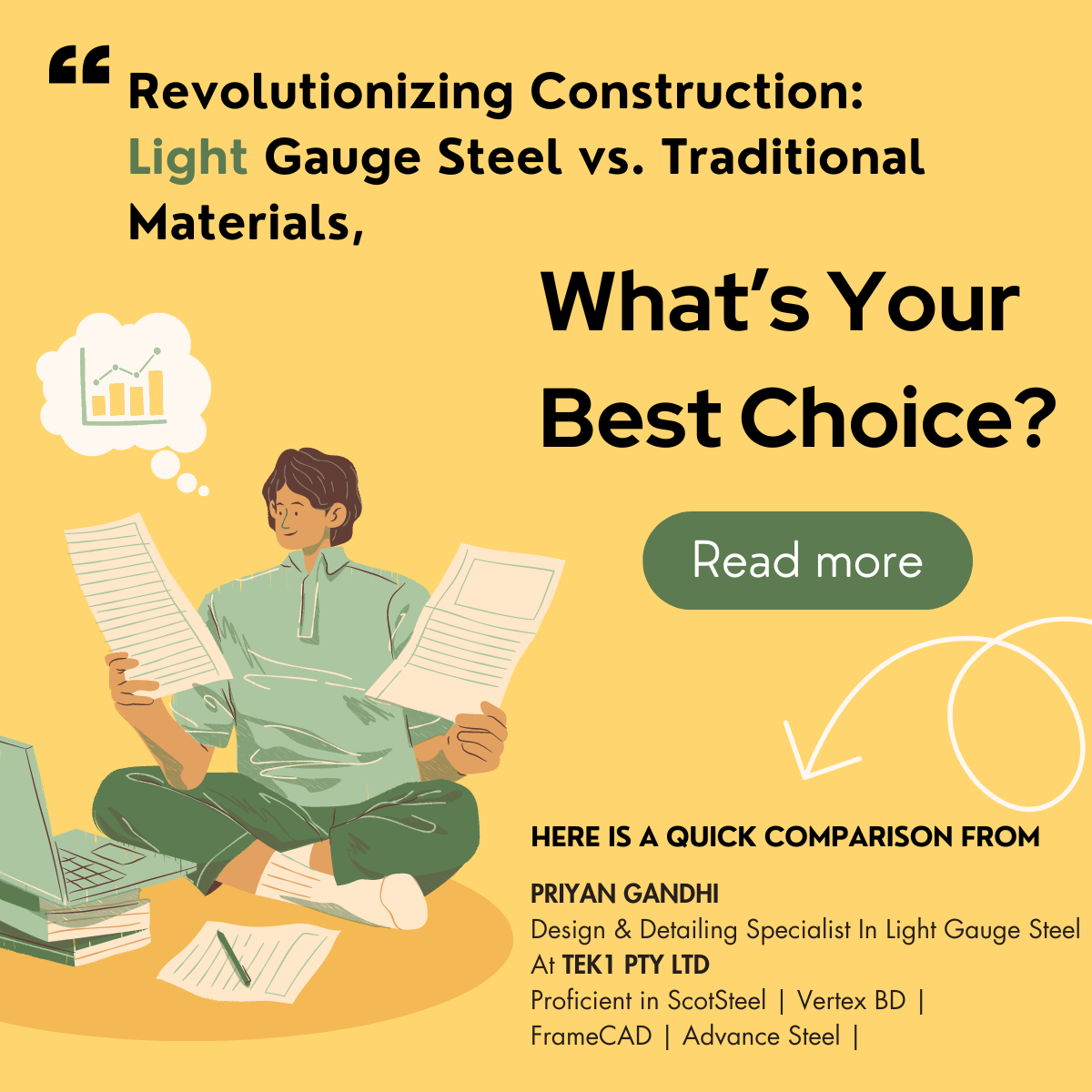
Leave a Reply